What is the Difference Between Filter Separator and Coalescing Filter?
Date: 2024-12-16 Categories: Industry information Views: 231

In various industrial applications, ensuring the purity of liquids and gases is crucial. This is where filtration systems come into play. Among the many types of filtration systems, filter separators and coalescing filters are two common types often used. While they serve similar purposes, they operate on different principles and are suitable for different applications. This article will delve into the distinctions between these two types of filters, exploring their functionality, applications, advantages, and more.
Introduction to Filtration Systems
Filtration systems are essential in maintaining the efficiency and longevity of industrial equipment. They remove contaminants from fluids, which can include water, oil, gas, and various chemical solutions. Contaminants can cause wear and tear, clogging, and even complete system failures if not properly managed. Thus, understanding the right type of filter for a specific application is key to maintaining operational integrity.
Understanding Filter Separators
Definition and Function
A filter separator is a multi-stage filtration system primarily used to remove solid and liquid contaminants from gas streams. It combines the functions of a mechanical filter and a separator into a single unit. This type of filter is highly effective in applications where both particulate and liquid contaminants are present.
How Filter Separators Work
Filter separators typically operate in two stages:
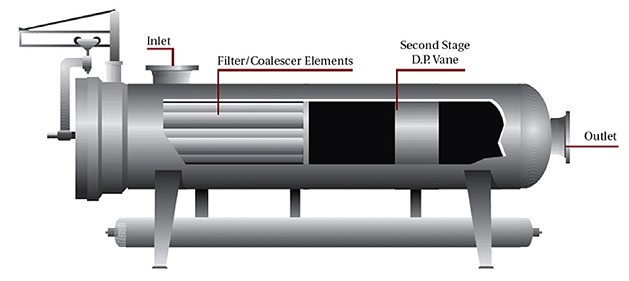
two stages
- First Stage - Filtration: The first stage involves a mechanical filter that removes larger solid particles from the gas stream. This filter element can be made from materials such as fiberglass, polyester, or other synthetic fibers designed to trap particulate matter.
- Second Stage - Separation: The second stage is where the separation of liquids from the gas stream occurs. This stage often involves a mist extractor or vane pack that causes the liquid droplets to coalesce and fall out of the gas flow due to gravity. The collected liquid is then drained away from the system.
Applications of Filter Separators
Filter separators are commonly used in the oil and gas industry, particularly in natural gas processing plants. They are also used in chemical plants, power generation facilities, and other industrial environments where gas streams need to be purified.
Understanding Coalescing Filters
Definition and Function
A coalescing filter is a specialized type of filter designed to remove aerosols, fine mists, and submicron particles from a gas or liquid stream. Coalescing filters are highly efficient at capturing very fine droplets of liquid and are often used in applications where high purity is required.
How Coalescing Filters Work
Coalescing filters work on the principle of coalescence, where small droplets of liquid are brought together to form larger droplets. This process involves:
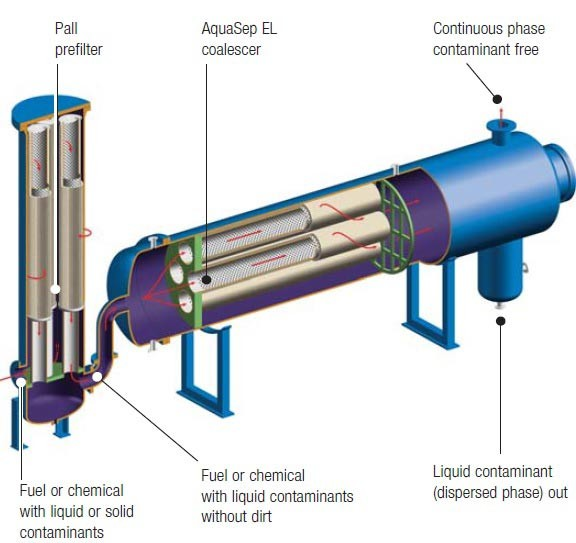
three stages
- First Stage - Pre-Filtration: The gas or liquid stream passes through a pre-filter to remove larger particles. This pre-filtration helps protect the coalescing element from clogging prematurely.
- Second Stage - Coalescence: The stream then flows through a coalescing element, which is typically made of fine fibers or porous materials. As the stream passes through, small droplets collide with the fibers, merge with other droplets, and form larger droplets.
- Third Stage - Collection: The larger droplets formed during the coalescence process are heavy enough to be removed from the gas or liquid stream. These droplets fall out due to gravity or are directed to a collection chamber where they can be drained away.
Applications of Coalescing Filters
Coalescing filters are used in various industries, including pharmaceutical manufacturing, food and beverage processing, and petrochemical production. They are especially valuable in compressed air systems, fuel systems, and any application where high levels of purity are critical.
Key Differences Between Filter Separators and Coalescing Filters
Purpose and Design
The primary difference between filter separators and coalescing filters lies in their design and purpose. Filter separators are designed for the dual purpose of removing both solid particles and liquid contaminants, while coalescing filters are specifically engineered to remove fine liquid aerosols and submicron particles.
Filtration Mechanism
- Filter Separators use a combination of mechanical filtration and gravity separation. The first stage removes solid particles, and the second stage separates liquid droplets through a mist extractor or vane pack.
- Coalescing Filters utilize the coalescence process to combine small droplets into larger ones, which are then removed from the stream. This method is highly effective for capturing fine mists and aerosols.
Applications
- Filter Separators are ideal for applications where both solids and liquids need to be removed from a gas stream, such as in natural gas processing or chemical plants.
- Coalescing Filters are best suited for applications requiring the removal of fine liquid aerosols and high levels of purity, such as in compressed air systems or pharmaceutical production.
Advantages of Filter Separators
Versatility
Filter separators offer versatility by handling both solid and liquid contaminants. This dual functionality makes them suitable for a wide range of industrial applications.
Efficiency
They are efficient in removing large quantities of contaminants, which helps protect downstream equipment from damage and reduces maintenance costs.
Longevity
By combining filtration and separation in one unit, filter separators can have longer service intervals and require less frequent maintenance compared to other types of filters.
Advantages of Coalescing Filters
High Purity Levels
Coalescing filters are capable of achieving high levels of purity, making them essential in applications where contamination can lead to serious issues, such as in pharmaceuticals or food processing.
Fine Aerosol Removal
They excel at removing very fine mists and aerosols that other types of filters might miss. This ensures a higher quality of the final product or processed gas.
Protection of Sensitive Equipment
By removing fine contaminants, coalescing filters help protect sensitive equipment from wear and tear, ensuring longer operational lifespans and reduced downtime.
Choosing the Right Filter for Your Application
When selecting between a filter separator and a coalescing filter, consider the following factors:

coalescing filter system
Nature of Contaminants
Determine whether your application involves solid particles, liquid aerosols, or both. Filter separators are suitable for handling both, while coalescing filters are specifically for fine aerosols and high purity requirements.
Required Purity Levels
Assess the level of purity needed for your process. Coalescing filters provide higher purity levels, making them ideal for critical applications.
Operational Environment
Consider the operational environment and the specific needs of your industry. Filter separators are robust and versatile, while coalescing filters are specialized for certain high-purity applications.
Maintenance and Longevity
Evaluate the maintenance requirements and longevity of the filters. Filter separators generally require less frequent maintenance, whereas coalescing filters may need more attention due to their high efficiency in capturing fine contaminants.
Common Industries Using Filter Separators and Coalescing Filters
Oil and Gas Industry
Both filter separators and coalescing filters are widely used in the oil and gas industry. Filter separators are employed in gas processing plants to remove contaminants from natural gas streams, while coalescing filters are used to purify compressed air and fuel systems.
Pharmaceutical Industry
The pharmaceutical industry relies heavily on coalescing filters to ensure the purity of gases and liquids used in drug production. These filters help maintain stringent quality standards and prevent contamination.
Food and Beverage Industry
In the food and beverage industry, coalescing filters are essential for removing fine mists and aerosols from processing streams, ensuring the final products are safe and high quality. Filter separators can also be used in certain applications to remove larger contaminants.
Chemical Manufacturing
Chemical plants utilize both filter separators and coalescing filters to maintain the purity of their processes. Filter separators handle mixed-phase streams, while coalescing filters ensure high-purity outputs for sensitive reactions.
Installation and Maintenance Tips
Proper Installation
Ensure that filters are installed correctly according to manufacturer guidelines. Proper installation is crucial for optimal performance and longevity of the filters.
Regular Maintenance
Perform regular maintenance checks and replace filter elements as needed. Regular maintenance helps prevent system failures and maintains filtration efficiency.
Monitor Performance
Use monitoring systems to keep track of filter performance and identify when maintenance is required. This proactive approach helps avoid unexpected downtime and extends the life of the filters.
Conclusion
Understanding the difference between filter separators and coalescing filters is essential for selecting the right filtration system for your application. While both types of filters serve to remove contaminants from fluids, their specific functions, mechanisms, and applications vary. Filter separators offer versatility and efficiency in handling both solid and liquid contaminants, making them suitable for a wide range of industries. On the other hand, coalescing filters excel in achieving high purity levels by removing fine aerosols and submicron particles, making them ideal for applications requiring stringent quality standards. By carefully assessing your filtration needs and considering the operational environment, you can choose the most appropriate filter system to ensure the efficiency, purity, and longevity of your industrial processes.
The size of your pulse jet bag filtration system will depend on the design you select.
You can follow the steps below to determine the most appropriate size of your filters.
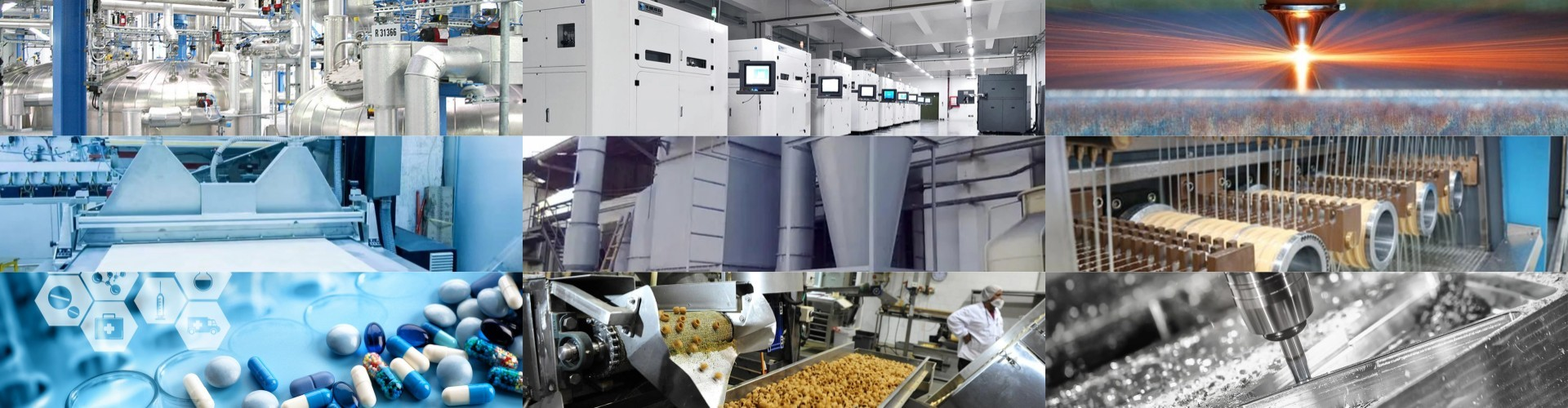