What is the difference between sintered plate filter and bag house filter?
Date: 2024-10-17 Categories: Industry information Views: 320
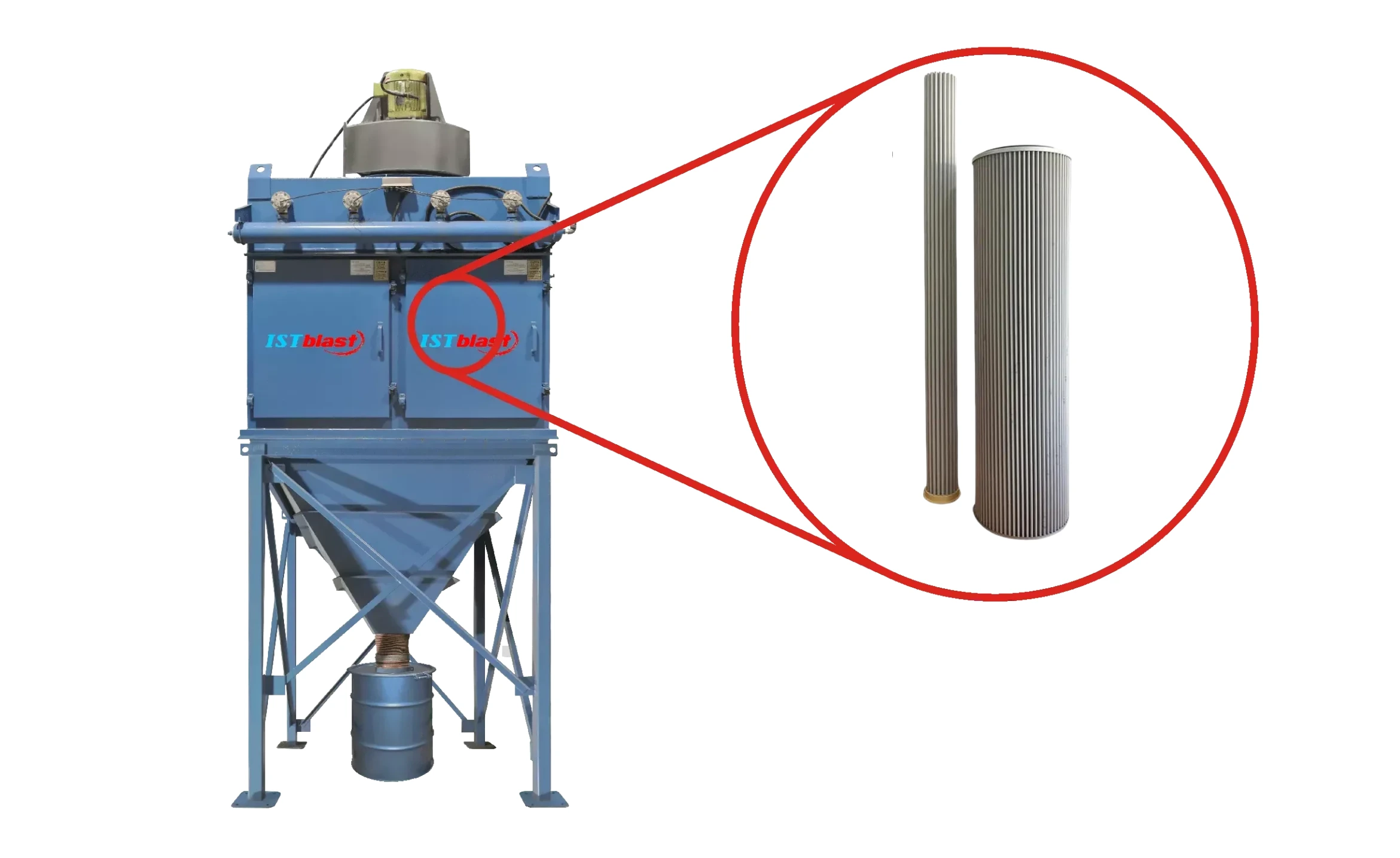
The sintered plate filter and the baghouse filter both serve as dust collectors, but they operate differently and offer distinct advantages depending on the application. Here’s a comparison between the two, with an emphasis on the sintered plate filter:
- Filtration Mechanism:
Sintered Plate Filter:
The filter uses rigid sintered polymer or metal plates. The sintering process creates a porous surface that allows for surface filtration, meaning particles are primarily captured on the surface of the filter.
Industrial filters are unique for their surface filtration and direct separation technology, which means that the particles are removed directly on the filter's surface without penetrating deeper into the filter media.
This mechanism ensures consistent and high-efficiency filtration, particularly for fine dust particles (down to the sub-micron range).
Baghouse Filter:
Baghouse filters use fabric or felt bags to capture dust particles. Filtration happens as dust-laden air passes through the bags, and particles are trapped either on the surface or within the fibers of the bag (depth filtration).
Baghouse systems are typically more suited for handling higher dust loads and larger particle sizes, but their filtration efficiency for very fine dust may not be as high as sintered plate filters.
- Filtration Efficiency:
Sintered Plate Filter:
Offers extremely high filtration efficiency, particularly for fine and sub-micron particles. The surface filtration ensures very low emissions, with dust separation efficiency typically greater than 99.9%.
Ideal for industries requiring high standards of air quality, such as pharmaceuticals, food processing, and electronics manufacturing.
Baghouse Filter:
Can achieve high filtration efficiency depending on the type of fabric used. Baghouse filters typically capture particles down to 1-10 microns, though some specialized bags can handle smaller particles.
Efficiency can decrease over time as dust accumulates within the bag and the filtration process relies on creating a dust cake on the surface for efficient filtration.
- Cleaning Mechanism:
Sintered Plate Filter:
The surface filtration design makes cleaning easier and more efficient. Reverse pulse air is typically used to clean the filter by blowing off dust particles from the surface, ensuring consistent filtration performance without clogging.
Due to the rigid nature of the sintered plates, there is no wear from cleaning cycles, contributing to the long lifespan of the filters.
Baghouse Filter:
Baghouse filters are also cleaned using methods like pulse jet cleaning, reverse air, or mechanical shaking. However, since the dust penetrates deeper into the fabric, cleaning may not be as efficient, and over time, the filter media can become clogged or damaged.
The bags experience wear and tear with each cleaning cycle, requiring more frequent maintenance and eventual replacement.
- Durability:
Sintered Plate Filter:
Extremely durable due to the rigid sintered construction. These filters are resistant to mechanical damage, can withstand high temperatures, and are often chemically resistant, depending on the material used.
The filter media does not degrade over time, meaning it has a significantly longer lifespan compared to fabric-based filters. In many applications, Sinter plate filters can last several years without needing replacement.
Baghouse Filter:
Fabric bags in baghouse filters degrade over time due to mechanical flexing during cleaning, exposure to heat, and abrasive dust particles. Bag replacement is often required at regular intervals, depending on the operating environment.
Bag materials can be chosen to resist specific conditions (e.g., high temperature, chemical exposure), but they will still wear out faster than rigid sintered filters.
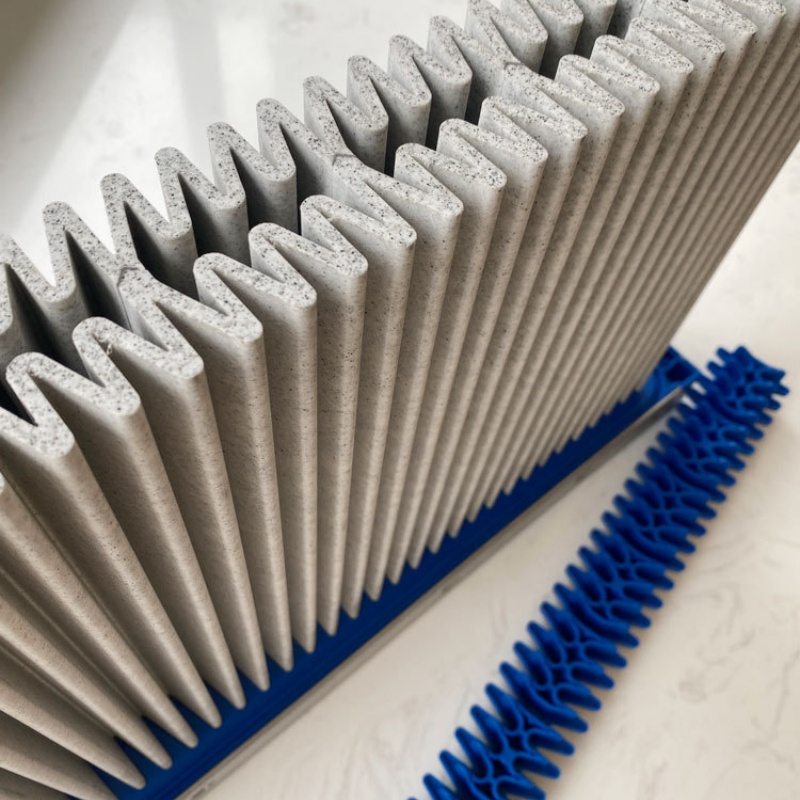
- Maintenance:
Sintered Plate Filter:
Requires less maintenance due to the durability and long lifespan of the filter plates. Since cleaning is efficient and doesn’t wear down the filter, these filters have low maintenance costs over time.
The sintered plates maintain high filtration efficiency throughout their lifespan without the need for frequent intervention.
Baghouse Filter:
Requires more frequent maintenance due to the need to replace worn-out bags. The cleaning process can also become less efficient as the bags age, which may lead to a decrease in filtration performance over time.
Regular monitoring and maintenance are necessary to ensure that the system continues to operate effectively.
- Cost:
Sintered Plate Filter:
The initial investment is higher due to the cost of manufacturing sintered plates, but the longer lifespan, lower maintenance needs, and high efficiency often make these filters more cost-effective over time.
The durability of the plates means that there are fewer costs associated with replacement parts and system downtime.
Baghouse Filter:
Lower upfront cost compared to sintered plate filters, but due to the frequent replacement of filter bags and more intensive maintenance, the long-term operational costs can be higher.
The need for ongoing bag replacement, cleaning systems, and potential system downtime adds to operational costs.
- Applications:
Sintered Plate Filter:
Suited for applications requiring high filtration efficiency, such as pharmaceuticals, food and beverage industries, chemicals, fine powder processing, and environments with stringent air quality requirements.
Preferred in industries where fine dust particles are a concern and where downtime for maintenance must be minimized.
Baghouse Filter:
Commonly used in heavy-duty industrial applications where large dust volumes are generated, such as cement production, mining, power plants, woodworking, and metal smelting.
Typically chosen for applications where coarse dust needs to be handled in large volumes.