Selecting the Optimal Industrial Filter: A Comprehensive Guide for Sales Engineers
Date: 2025-02-22 Categories: Industry information Views: 125
Choosing the right industrial filter is essential for ensuring operational efficiency, reducing downtime, and maintaining the longevity of equipment across various industries. Sales engineers play a crucial role in understanding client needs and recommending the most suitable filtration solutions.
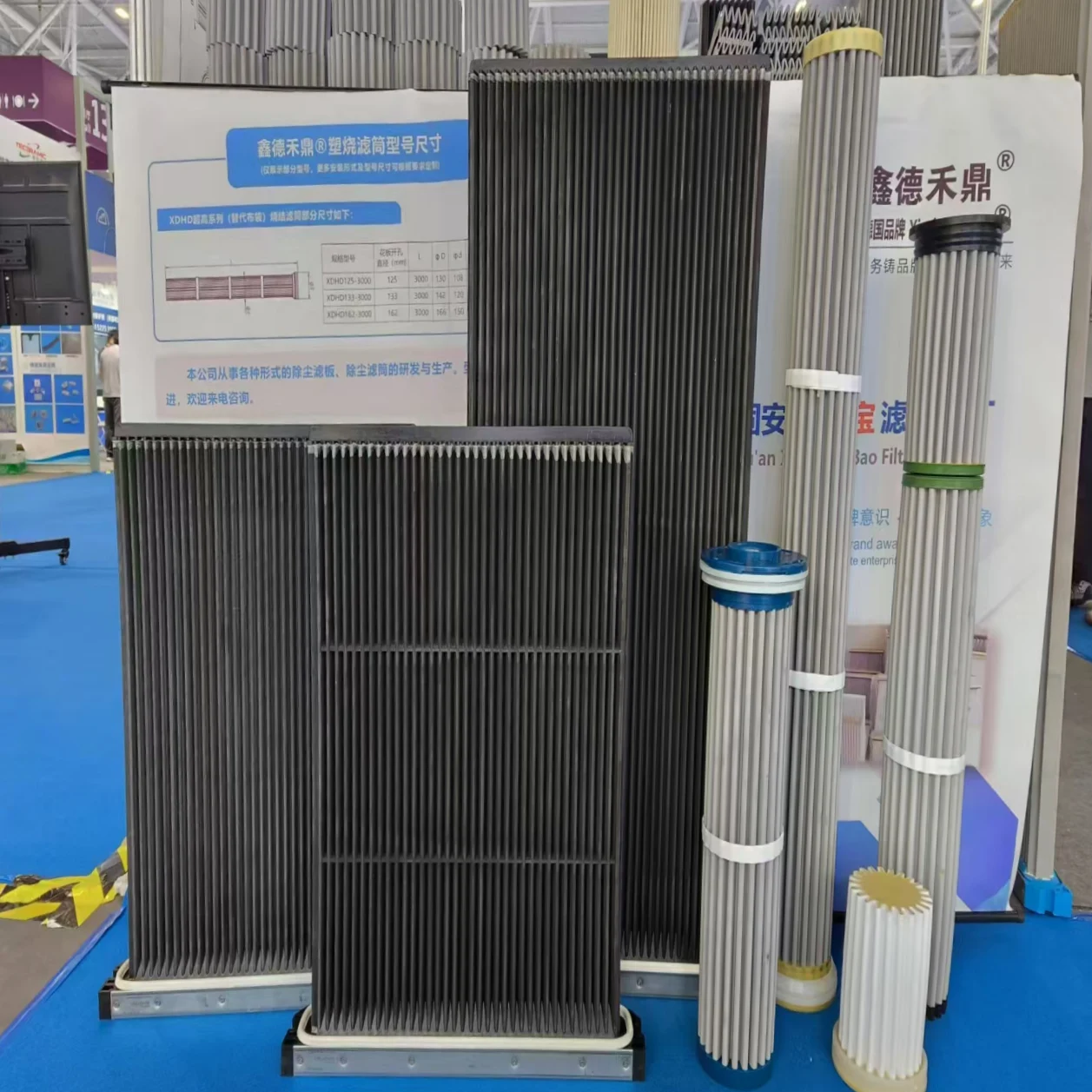
1. Understand the Application and Requirements
- Industry Type: Different industries have specific filtration needs. For example, food and beverage industries require sanitary filters, while chemical industries focus on removing hazardous substances.
- Flow Rate and Pressure: The filter must handle the system's flow rate and pressure without causing disruptions.
- Temperature Range: Select filters that can withstand the operating temperature of the system.
- Type of Contaminants: Identify the contaminants to be filtered, such as dust, particles, chemicals, or oils.
- Regulations and Standards: Ensure compliance with industry standards such as FDA, ISO, or GMP.
2. Types of Industrial Filters
Different filters serve various functions:
- Bag Filters – Used for liquid filtration in food processing, wastewater treatment, and chemical industries.
- Cartridge Filters – Provide high-precision filtration for applications such as pharmaceuticals and electronics.
- HEPA Filters – Capture fine airborne particles and are used in cleanrooms and hospitals.
- Magnetic Filters – Remove ferrous metal particles, often used in the automotive and manufacturing sectors.
- Vacuum Filters – Handle slurries and suspended solids, commonly used in wastewater treatment and mining.
- Dust Collectors – Remove airborne dust in construction, cement, and woodworking industries.
- Carbon & Activated Filters – Absorb odors, gases, and chemicals in air and water treatment applications.
3. Filter Efficiency and Micron Rating
The micron rating indicates the smallest particle size the filter can capture:
- 100–500 microns – Coarse filtration for large particles like dirt and debris.
- 1–100 microns – Fine filtration for smaller contaminants.
- Below 1 micron – Ultra-fine filtration for applications such as pharmaceuticals and medical devices.
4. Material Compatibility
Filters must be compatible with the substances they will filter:
- Polypropylene, Polyester, or Nylon – General-purpose applications.
- Stainless Steel – For high temperatures and corrosive environments.
- PTFE (Teflon) – Chemical-resistant applications.
- Ceramic – Extreme temperature or harsh conditions.
5. Filter Lifespan and Maintenance
- Service Life: Consider whether the filter is disposable or cleanable.
- Ease of Maintenance: Look for filters that are easy to replace or clean.
- Maintenance Costs: Choose long-lasting filters to minimize replacement costs.
6. Cost vs. Efficiency Trade-Off
- Initial Cost: Cheaper filters may have higher long-term costs due to frequent replacement.
- Operating Costs: Ensure filters do not increase energy or operational expenses.
- Replacement Frequency: Longer-lasting filters may offer better value.
7. Environmental Considerations
- Energy Efficiency: Filters with low energy consumption can reduce operating costs.
- Waste Management: Consider disposal and recycling options.
- Sustainability: Choose filters made from eco-friendly materials.
8. Filter Manufacturer and Brand
- Certifications: Ensure compliance with industry standards.
- Warranty and Support: Look for manufacturers that provide strong customer service.
- Reputation: Choose reliable brands with proven industry experience.
9. Customization and Special Requirements
- Custom Filtration Solutions: Some applications require tailor-made filters.
- Modular Systems: Allows for easy upgrades and adjustments.
10. Testing and Validation
- Pilot Testing: Test filters in real-world conditions before full implementation.
- Post-Installation Testing: Verify that the filter meets performance expectations.
Conclusion: The Sales Engineer’s Role
Sales engineers should take a consultative approach by:
- Understanding client needs through detailed discussions.
- Providing technically sound recommendations based on system requirements.
- Offering additional services like maintenance support.
- Using data-driven insights from testing and case studies.
By following this guide, sales engineers can effectively recommend the best industrial filters to optimize performance, efficiency, and cost-effectiveness for their clients.