Sinter-plate dust collector uses a unique wave type sinter-plate filter element to replace the traditional cloth bag. Because the sinter-plate is a rigid structure, will not deform, and has no framework wear, it has a long service life. Under some working conditions, its service life is more than 10 times that of the cloth bag.
Due to the deep treatment of the surface of the sinter-plate, the pore diameter is small and uniform, with hydrophobicity, and it is not easy to adhere the dust with high water content, so the sinter-plate dust collector is the best choice when dealing with the dust with high water content and fibrous dust. In addition, as the high-precision manufacturing process of the sinter-plate maintains a uniform micron aperture, it can also handle ultra-fine dust and high concentration dust.
The inlet concentration of the bag filter is generally less than 20 g / m3, while the inlet concentration of the sinter-plate dust collector can reach 500 g / m3. The utility model can simplify the two-stage dust collection into the first stage dust collection, which is not only convenient in process, but also can reduce the cost and energy consumption and reduce the floor area and space pipeline.
Features/Advantages
(XDHD) are specifically designed for high filtration efficiency and low pressure drop. The monolithic design is also very strong and durable, making it ideal for a variety of applications.
Product Advantages:
Longest service life of sintered plates up to 10 years
Long service life, relatively low maintenance and consumables costs
Optimized geometry reduces pressure drop
Increased pleats in each chamber significantly increase filter area
Constant pressure drop keeps airflow constant, helping to improve equipment efficiency
Surface filtration for high separation efficiency
Monoblock sintered plate design for compact rigidity
Suitable for abrasive dusts
Completely fiberless filter media, ideal for product recovery
Can be cleaned, recycled, and refurbished
Can be provided with anti-static or non-anti-static sintered plates
Can be installed from either dirty gas or clean gas side
Can be installed horizontally or vertically
Direction of installation
Depending on the individual application and process requirements horizontal or vertical installation is possible.
1 Clean gas-side installationInstalling
the filter elements from the clean gas side enables optimal and clean access to the filter elements and provides highest possible protection for the personnel.
2 Raw gas-side installation
Installing the filter elements from the raw gas side usually allows a direct and optimal revision of the raw gas area. It requires no additional height above the filter system for servicing the filter elements.
pure surface filter
The sinter plate filter have a PTFE coating on the PE basis, so do not need dust cake to block the other dusts.
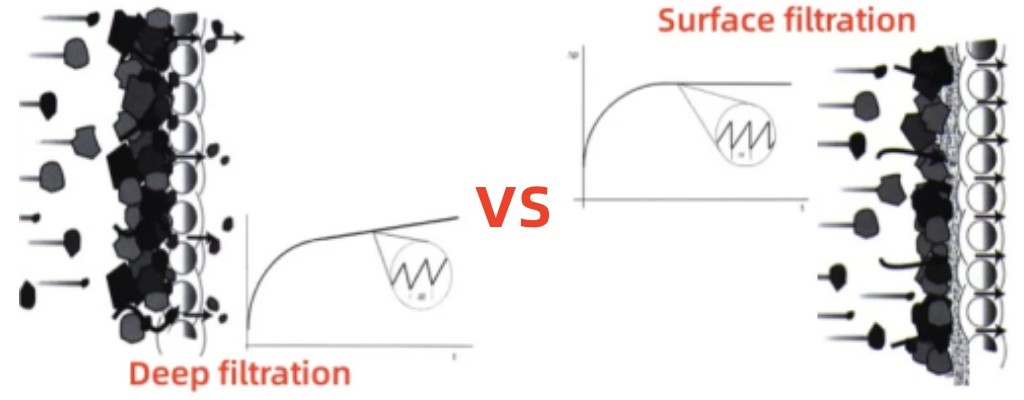
When the pulse-jet working, the efficiency will not influenced by the original conditions.It is called surface filtration.
The advantages of Herding filters with surface filtration include:
- High Efficiency Filtration: Surface filtration technology efficiently captures and separates particles on the surface of the filter media, providing effective filtration and removing fine particles effectively.
- Low Pressure Drop: Surface filtration typically results in lower pressure drops compared to depth filtration, leading to reduced energy consumption and lower operational costs.
- Long Service Life: Surface filters often have extended lifespans as they are less prone to clogging, and maintenance is relatively simple, minimizing downtime and maintenance expenses.
- Wide Applicability: Surface filtration technology is suitable for various industrial applications, including dust collection, gas purification, liquid filtration, offering flexibility and versatility.
- Versatility in Particle Capture: Surface filtration effectively captures particles of various sizes and shapes, ranging from fine particulates to larger particles, making it suitable for a wide range of applications.
Technical Data
Picture | Item No. | A | B | C | D | D₂ | E | n | Filter area |
mm | mm | mm | mm | mm | mm | ㎡ | |||
![]() |
XDHD750-9 | 565 | 490 | 424 | 758 | 720 | 551 | 8 | 2.3 |
XDHD1200-9 | 565 | 490 | 424 | 1203 | 1165 | 551 | 8 | 3.7 | |
XDHD1500-9 | 565 | 490 | 424 | 1495 | 1457 | 551 | 8 | 4.7 | |
XDHD750-18 | 1047 | 966 | 901 | 755 | 705 | 1035 | 17 | 4.7 | |
XDHD1200-18 | 1047 | 966 | 901 | 1200 | 1150 | 1035 | 17 | 7.6 | |
XDHD1500-18 | 1047 | 966 | 901 | 1500 | 1450 | 1035 | 17 | 9.4 |